Other concerns were voiced as well, including issues like scheduling, finding raw materials, improving quality, increasing productivity and so forth. Others want to reduce their inventories and increase their flexibility through lean manufacturing.
Some are simply struggling with their own growth. “We are running out of space,” said a manufacturing engineer at a mid-sized Canadian job shop.
We deliberately did not ask questions about profits in this survey. Many of the respondents wouldn’t necessarily have access to that kind of information. Others work at large OEMs whose profits are largely dependent upon factors outside of their gear manufacturing operations. But it’s clear from the comments of many of the respondents that, although they are extremely busy, it doesn’t necessarily follow that they’re also extremely profitable.
Reading through their comments, you get the sense that gear manufacturers are feeling squeezed, in more ways than one. Some are squeezed by space constraints. Others are squeezed by pricing. Still others are squeezed by their customers’ demands for higher productivity, lower prices and improved quality.
But squeezing the most out of the least is the task of modern manufacturing. Despite the many challenges facing them, you also get the sense from reading their comments that the gear industry is not only up to the task, but also hopeful about its future.
What Other Factors are Presenting Significant Challenges to Your Business?
“Although we have experienced a nice increase in sales in the last 18 months, there is still a fear that the industry could go into a downturn again…The fun of what would be coming in the door next is being replaced by the dread of ‘How can we meet these ridiculous deliveries on parts we quoted months ago and now are suddenly HOT because the customer waited so long to order.’”
-—a manufacturing production worker at a Michigan job shop
“Coping with changing demands on products. Reducing stock levels with a view to becoming leaner.”
-—design engineer at a U.K. manufacturer of gear drives
“Failure of society/industry to shake negative perceptions about machining as a career, thus difficulty in finding and hiring excellent, intelligent help.”
-—corporate executive at a small U.S. manufacturer of automotive powertrain products
“Increased competition, but domestic.”
-—a manufacturing engineer at a major U.S. automotive transmission plant
“Keeping up with rapid growth and demand.”
-—a quality control worker at a U.S. manufacturer of mining equipment
“Meeting the ever-increasing demands for quicker deliveries and reducing lead times, coupled with price reduction requests. Many customers’ expectations have gone beyond being unreasonable.”
-—corporate executive at a mid-sized Illinois job shop
“More and more companies which were not gear producers 10 years ago are now getting into the gear business.”
-—employee at a mid-sized Michigan job shop
“Not just the cost of gear steel, but availability; getting forgings into the plant.”
-—production worker at a large U.S. manufacturer of industrial gearboxes
“Suppliers being able to meet our scheduled ramp-up and our quality requirements.”
-—manufacturing engineer at a major U.S. automotive transmission plant
What are Your Company’s Most Significant Manufacturing/Engineering Challenges for 2007?
“Find people with enough skill on gears.”
-—manufacturing engineer at a small California job shop
“Bringing the best manufacturing practice to produce world-class gear products. Implementing six sigma and TQM culture into the organization.”
-—corporate executive at a small Indian job shop serving the construction market
“Cost reduction to compete with foreign products.”
-—production worker at a small U.S. manufacturer of motion control products
“Creating good scheduling for production, to create better on-time delivery.”
-—production worker at a large U.S. job shop serving the aerospace industries
“Design and prototype products in a shorter time period with the same resources.”
-—design engineer at a major U.S. manufacturer of construction/off-highway equipment
“Expansion: double production capacity without losing focus on cost optimization.”
-—corporate executive at a major European manufacturer of industrial gearboxes
“Finding and retaining skilled labor.”
-—corporate executive at a mid-sized New York job shop
“Increasing the production by at least 10% while reducing the manpower by 2-5%.”
-—manufacturing engineer at a major Indian automobile manufacturer
“Keeping production costs low and keeping our competitive edge against foreign competition.”
-—marketing & sales worker at a mid-sized job shop in Malaysia
“To reduce price without affecting quality and delivery.”
-—quality control worker at a major U.S. aerospace job shop
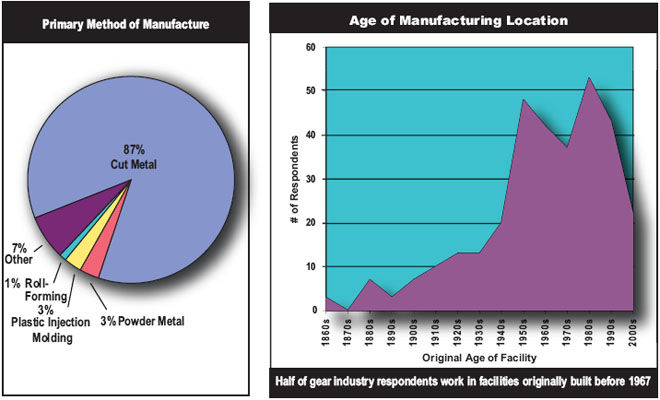