“Impact of coatings on gears and how they affect the performance of lubricants is a growing concern. The use of different coatings can have different performance results, resulting in different formulations, which could lead to a need for more specialized lubricants.”
“EV push and market acceptance, mining expansion in North America, political support for mining given EV push.”
“Customers are developing applications that will require gearing that has a smaller footprint, requires less energy/has better efficiency, and has greater precision.”
“Ongoing shortage of factory replacement gears and long lead times.”
“Lack of skilled gearing engineers knowledgeable in both design and efficient/effective manufacturing of gears. Transition from ICE to electric drives requiring a different gear and gearbox design (higher input speeds). Conventional gears are commodities and will be produced by low-cost countries due to higher steel and labor costs in the U.S. (except for prototypes and repairs).”
“Electrification of cars.”
“Electrification.”
“China/Asia competition. Low cost of production.”
“Vehicle electrification.”
“We should stop making the parts we lose money on and be more selective about the new parts we take on. Currently grasping to make anything.”
“The new technical developments of my company will support our market position and will help us to grow more in the following years.”
“Improvements in powdered metal options.”
“Gear manufacturing for e-vehicles worldwide.”
“Economy ups and downs, electrification, materials change, heat treatment advances.”
“Materials cost. processing innovations.”
“Torque density (increased torque in smaller packages) and overall weight.”
“Finish hobbing and gear grinding will be the focus. Gear shaving is going to reduce a lot.”
“Gear train in both transmission and engine are reducing as EV is taking over, but ICE will continue to be dominant with hybrids competing with EV.”
“The lack of capabilities in the U.S. and on-time delivery across the board is only showing minimal improvement.”
“Competitiveness arising from China and India.”
“No new people coming into the business as technicians, engineers or on the shop floor. The so-called CEO/Operations Manager/CFO would rather ship the work and knowledge overseas or across borders than keep home.”
“Automotive: Electric cars mean fewer gears are required per car.”
“Cost and overseas competitors.”
“Gears for electric drive units without noise.”
“China.”
“Employees & cybersecurity, healthcare.”
“Change in technology to hybrid and EV.”
“Global uncertainty, disruption of supply chains, economic recession.”
“New workers and financing.”
“Lack of personnel and lack of resources to train them.”
“Waviness on the gear tooth originating at the hard finishing operation resulting in NVH topics at EoL or in the field.”
“Ever-increasing demands on tool precision while not allowing for appropriate price increases, among others.”
“Continued investment in new plant and equipment, experienced employees.”
“EV transmission shift from IC segment. Less noisy gears, gear microgeometry evolution.”
“Upgrading in machine and tooling technologies, the volatile alloy steel markets.”
“Energy change in vehicles.”
“Upgrading equipment/CNC gear equipment.”
“Electrification of the drivetrain.”
“Electrification in agricultural implements.”
“Cost competitive gear manufacturing, low noise gear design, high power density gears.”
“Continuing supply chain issues for raw materials.”
“Geopolitical unrest in the world.”
“Constant pressure to keep prices low. The whining from customers is incessant.”
“Integration of sensors in gears.”
“Silence, reliability, availability, delivery, cost.”
“Fully automated drives with self-locking gears.”
“Transport electrification.”
“General lack of knowledge by most of our customers in the way they treat gearboxes in their plant. Overloading and lubrication issues.”
“EV gear boxes including differentials.”
“EV gear systems.”
“Power skiving, scudding process is getting momentum over shaping, broaching and penetration will increase with increasing mobility volumes.”
“Inspection and various evaluation techniques.”
“Design optimization of gears and gearbox components for minimal global competitive cost, having higher torque rating without compromising the quality, ensuring the reliability and durability of the gearbox.”
“International relations and geopolitics.”
“Becoming carbon neutral.”
“Hardening methods to address material distortion. Hardened material machining for better gear accuracy. Functional and manufacturability vs encompassing requirements that tend to be interpreted in many different ways.”
“Aerospace is very busy.”
“Customers want more data, faster lead times and lower price points.”
“Improvements in manufacturing gears, especially surface condition.”
“High quality gears will be the trend, and the metrology aspect will be relevant.”
“Big influence of IT.”
“The main trend that is positively affecting our business is the trend towards electrification in the automotive industry. Great opportunities are opening up for new technologies for the manufacture of electric cars.”
“The electrification trend.”
“Offshoring of gears due to labor costs. Cost of running a manufacturing company in California is just too expensive to continue in this state.”
“Rising steel costs, lack of skilled manpower, increased material costs, etc.”
“Continued strong oil and gas market.”
“EV.”
“Increasing E-mobility for bikes, cars, trucks.”
“Automation is becoming a very important consideration in gear manufacturing. 3D printing is going mainstream and will be utilized in gearing. EV market is evaporating due to poor performance and lack of interest.”
“We are not state-of-the-art. We are unaffected [by most trends].”
“Additive manufacturing of gears and polish grinding of gears.”
“Health of automotive industry.”
“The use of 3D printing and how gears could be produced with it.”
“More of our customers are purchasing from outside of the USA.”
“Skilled labor shortage and productivity opportunities.”
“Metrology technologies for both gear manufacturing and gearbox instrumentation.”
“AI (artificial intelligence). Investment in research, development and innovation.”
“Noise reduction.”
“American election cycle and political instability due to nationalistic Republican front runner who seems more interested in protecting himself from the consequences of his actions than providing leadership.”
“Major impact of electrification on automotive will request more sophisticated and higher quality class on gear supply than traditionally required.”
“Government instability.”
“Done-in-one automation! Now we can deburr and finish the gears on the CNC using ceramic fiber brushes.”
“Trends in gearboxproduction and gear manufacturing shifting away from North America in favor of global low-cost countries. U.S. OEM refocus on gearbox service and refurbishment: Success stories, winning strategies, etc.”
“Economy.”
“Reduced lead times, with quality products at a fair price.”
“Gear quality.”
“Macro economy and where interest rates go.”
“AI and EV everything and keeping info current.”
“Lack of help available.”
“Election years always bring a certain amount of uncertainty. Automation continues to be a focus. Attracting and retaining talent is key, especially CNC machinists.”
“Skilled labor is still a problem.”
Forest City Gear Examines 2024 Machine and Personnel Investments
Kika Young, president, and Jared Lyford, director of operations at Forest City Gear recently discussed the state-of-the-gear industry from the job shop perspective. The greatest challenges facing the custom gear manufacturer includes the rising costs of perishables, consumables, etc. as well as the ability to find skilled labor. Three priorities FCG will focus on includes:
- Utilization of its direct labor force to be monitored and measured through more advanced tracking technology.
- Investment in new equipment (this will be further vertical integration and will include a mill-turn as well as inspection technology) this helps to consolidate the vendor base and therefore lower the risk of outside suppliers.
- Managing rising customer sophistication and the costs that come with it.
“As our customers get more sophisticated and have higher inspection requirements, higher program requirements, demands for export control and cyber security—keeping up with pricing to capture these overhead costs can be difficult.”
-Young
In terms of machine technology and utilization, the gear manufacturing community is evolving.
“From the perspective of a job shop, you see alternate solutions for gear manufacturing, such as multitasking machines, coming into play for the lower volume prototype opportunities—thus making it less advantageous for a higher margin loose gearing manufacturing to capitalize on these smaller run opportunities. One aspect to secure new customers is providing front-end value and this type of machine capability has cut out some of this value-add from a DFM perspective,” Lyford said.
In addition, Lyford explained that the power of engineering software (SolidWorks, Inventor, etc.), has allowed a younger/less experienced generation of engineers to design parts which are more complex and therefore much more difficult to produce—thus creating even more need for the expertise of the custom gear manufacturer. Overly complicated designs due to more capable software and less experienced design engineers are causing this overall lack of design for manufacturability.
FCG will continue to focus on building its own workforce and training/promoting from within the organization. Young discussed the importance of getting new employees in front of machine tools to enhance their technical skillsets.
“There are several different aspects to this the first of which would be learning style. It is helpful and advantageous for many visual and hands-on learners to see a task in person and complete it themselves to fully understand the mechanical concept. There is a great deal of opportunity when you’re focused on hands-on training where theory is in practice. Conceptualizing an idea out of a textbook is a lot easier when it is physically happening in front of you. It is easier to synthesize the information in front of you when you understand the practical (and not just theoretical) application,” Young added.
FCG is planning to expand its presence in manufacturing through organizations such as the National Tooling & Machining Association, AGMA, IMEC and the local chamber of commerce.
Both Young and Lyford see several emerging technologies influencing gear manufacturing:
“As far as additive manufacturing there is an opportunity in 3D printing primarily for workholding and tooling from our perspective,” Lyford said. “Additionally, we see it as an advantage to create protypes models for our engineers as they begin to do process planning for new and complicated parts.”
FCG was an early adopter of robotics and automation on its gear cutting equipment.
“Within our business we see the ability to leverage robotics and cobots to offload some of the basic part loading and material handling operations which today are primarily done by our direct labor force. Cobots would allow us to train our operators to focus on more delicate and/or feature critical activities.”
-Young
forestcitygear.com
|
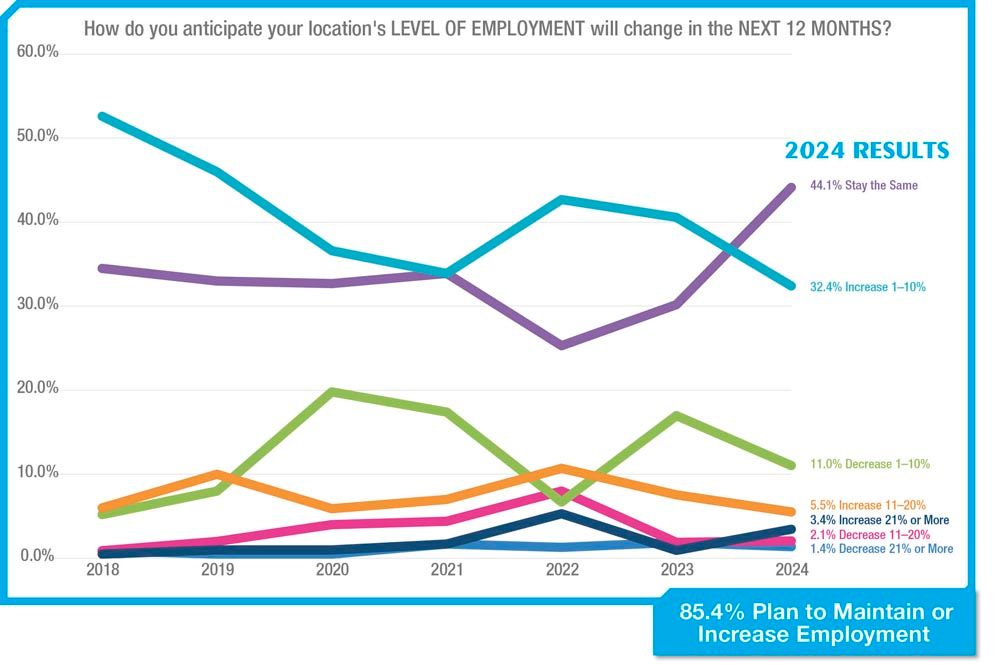
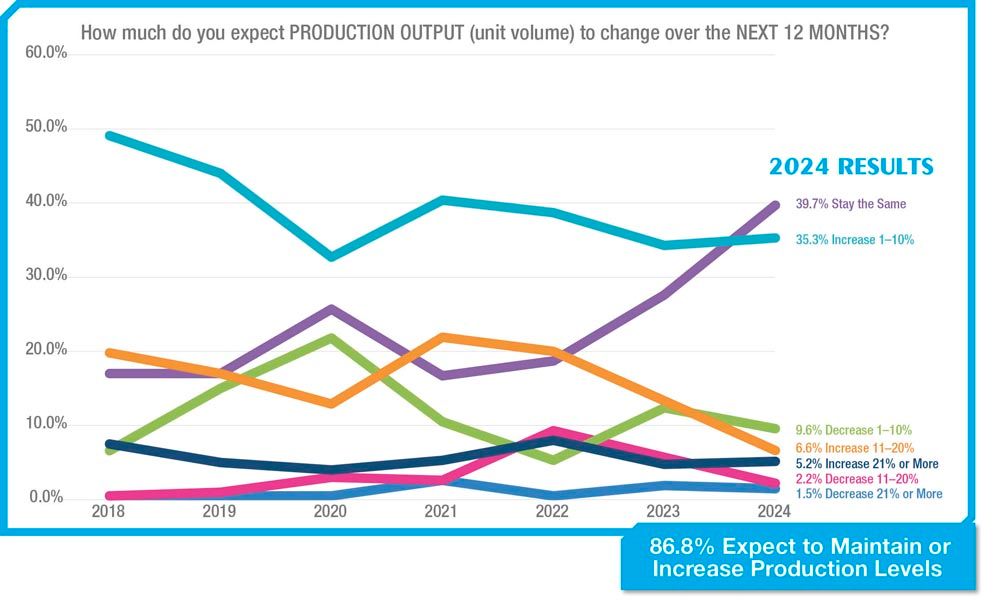
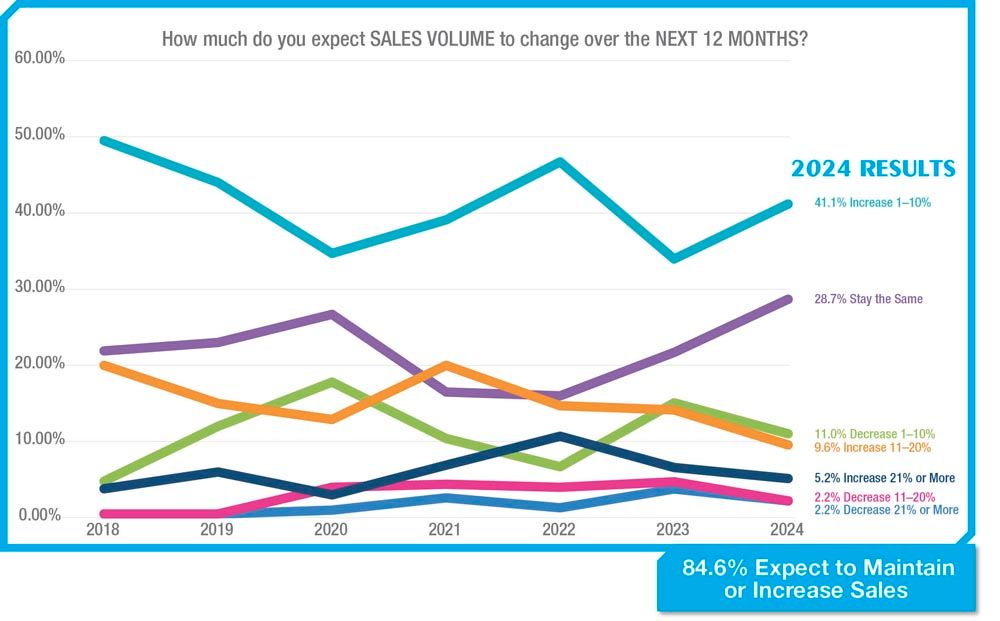
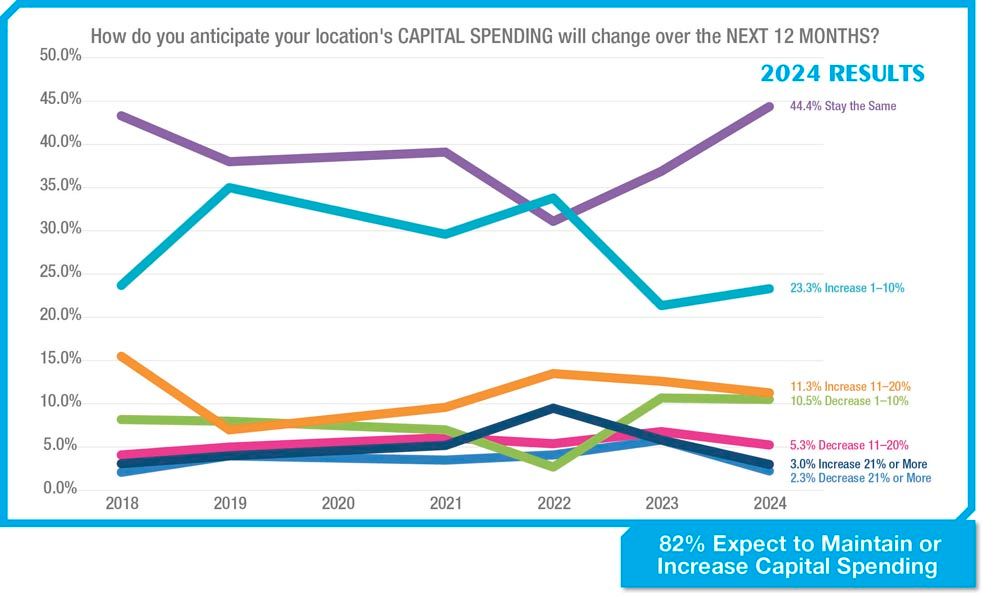
The View from Here
Aaron Fagan, Senior Editor
In 2024, machine tool companies anticipate challenges such as global insecurity, supply chain disruptions, and adapting to the electric vehicle market. Gleason, GMTA, Kapp Niles, Helios Gear Products, MTB, Nidec Machine Tool America, and Star SU express concerns about geopolitical issues, EV market adaptation, balancing current orders and new projects, softening demand, and communication challenges. Optimistically, they foresee opportunities in stable industries, economic growth, onshoring, and increased demand for gear manufacturing. Training programs focus on gear education and apprenticeships, while IIoT and Industry 4.0/5.0 remain significant. Workforce development solutions aim to bridge the skills gap. E-mobility’s trajectory varies, and companies emphasize minimizing carbon footprint and evaluating sustainable practices. Concerns include the aging workforce, political landscapes, and ongoing challenges like overregulation and declining production. Nidec highlights involvement in additive manufacturing and strategic acquisitions for continued growth in 2024. Overall, the industry faces a mix of challenges and opportunities, with a keen eye on global, technological, and political dynamics.
What are the most significant challenges 2024 will present to your machine tool company?
Global insecurity with the continuing crisis in Ukraine and the Middle East, potential crisis and dangers to global supply chain, US elections may also bear risks and opportunities. Chinese economic development continues to drive/influence world demand.
—Christian Albrecht, Chief Marketing Officer, Gleason Corporation; gleason.com
The most significant challenges for GMTA in 2024 include adapting our product portfolio to the EV market, addressing continued supply-chain disruptions (long lead times), and understanding how AI and other technological advancements can be incorporated into our business model.
—Claudia Hambleton, Office Manager/Corporate Treasurer, GMTA; gmtamerica.com
From a global perspective, the most significant challenge will be managing deliveries from a strong order backlog, similarly the follow-up on installation requirements with the ability to support ongoing field requirements. It is a balancing act that we must support the current installation base with the demand on our organization to install and successfully launch new projects.
—Shane Holllingsworth, Vice President Sales, Kapp Niles; kapp-niles.com
2023 was a very strong year for us, so I expect some rebound from our customer base, meaning a softening of machine tool demand. As a machine tool distributor, we continue to be challenged by keeping our manufacturing customers up to speed with the latest technological options available to them. There’s just a lot of communication noise that every individual must combat in today’s always-connected world, so communicating technical update information to manufacturers can be challenging.
—Adam Gimpert, President, Helios Gear Products; heliosgearproducts.com
Keeping up with the global demand for gear-cutting machines and metrology, as well as automation solutions, remains the biggest challenge for our Liebherr production program. Over the past few years, the industry has seen delivery times elongated due to supply chain issues, but also due to the increasing market demand for our gear machines and technology. 2024 will continue with strong demand—and we are ready for that challenge. A further challenge is always trying to apply some of the new ideas and gear technology developments into the new customers workpieces (EV) and applications, due to their high-quality demands and sometimes unique features (special chamfers, for example).
—Bernd Rösch, Head of Testing, Gear Technology, Liebherr; liebherr.com
I can’t help but sense “a disturbance in the force.” While the economy has withstood a lot over the last few years, one must wonder about the impact deficits, wars, and borders will have going forward. It doesn’t take much to throw a monkey wrench into even our great, very resilient economy. One has only to look at how supply chains seized up and inflation went through the roof. Much is riding on the outcome of the elections this year, and how our nation goes forward in the face of mounting threats overseas.
—Kenneth Flowers, Owner and President, Machine Tool Builders (MTB); machinetoolbuilders.com
The market continues to demand higher quality parts, shorter cycle times, and, as always, higher efficiency/lower costs. Nidec Machine Tool America (NMTA), as part of the dynamic and fast-growing Nidec group of companies, will continue bringing innovative new solutions to the high-volume gear production market, such as the new CF26A cut chamfer machine. Getting the word out about our advanced solutions is a welcome challenge.
—Dwight Smith, Vice President, Nidec Machine Tool America (NMTA); nidec-machinetoolamerica.com
For our machine tools, we see continuous demand for e-mobility applications driving larger, higher speed gears, tighter tolerances, and an impact on noise reduction as part of a growing emphasis on gear face chamfering applications.
—Andreas Blind, President, Star SU LLC & John O’Neill, Engineering Manager, Gear Tools, Star SU LLC; star-su.com
What are you optimistic about for 2024?
While e-drive growth continues, some manufacturers reconsider options including rather classic approaches. Strong aerospace industry, stable construction, agricultural, and transportation markets. Although production is forecasted to decline in many markets, we believe that we are well-positioned to overcome these looming challenges.
—Christian Albrecht, Gleason
The possibilities introduced by AI and bringing new partners to the US market.
—Claudia Hambleton, GMTA
Onshoring continues to be a common thread as supply chains adjust in a post-pandemic world. Helios is uniquely situated to bring world-class machine tool solutions to North American and European manufacturers.
—Adam Gimpert, Helios
With the introduction of several series of gear machines, including FlexChamfer for gear hobbing, and ChamferCut IG for the skiving process, and further process monitoring (out of our digitization packages) for gear grinding we’ve several new developments for increasing productivity in gear machine shops.
—Scott Yoders, Vice President Sales, Liebherr Gear and Automation Technologies; liebherr.com
While the global economic conditions are uncertain, and seemingly one crisis after another around the world leads off the nightly news every day, I remain stubbornly optimistic. If current economic conditions, particularly supply chain issues, have told us anything post-pandemic, it’s that we’ve got to start producing more here at home. We’re expecting more robust demand as a result—perhaps not this year, but certainly in the years to come.
—Kenneth Flowers, MTB
The economic trends are encouraging; inflation is moderating, and businesses have cash for capital projects. Re-shoring continues to bring more gear-making to the US, and NMTA is well-positioned to serve the market. I expect 2024 to surpass 2023 in economic growth and sales for NMTA.
—Dwight Smith, NMTA
While we foresee a softening in the overall manufacturing industry, we feel optimistic that gear-tool demand will continue to remain strong driven by reshoring and e-mobility applications.
—Andreas Blind & John O’Neill, Star SU
What will 2024 training programs look like from the machine tool industry?
Gleason continues to educate the industry with the broadest program of basic and advanced gear design, manufacturing, and metrology topics, including the latest gear technology trends. In May 2024, Gleason will present its yearly webinar highlight “E-Drive Days,” and offer in-person gear technology seminars in specific markets throughout the year. In addition, Gleason will continue to run its highly acclaimed live Gear Trainer Series and has introduced more Gear School Classes in the US and Germany, extending to customers’ areas—we call it the “Gear School on the Road.”
—Christian Albrecht, Gleason
I see further implementation of apprenticeship-style opportunities. Due to the skills gap and the expected increase in employment, companies will need to take on the task of bridging education with real-world needs.
—Claudia Hambleton, GMTA
Helios has expanded its education and training offerings to supplement its 33-year-old Chicago-based “gear school,” so manufacturers can now send personnel to regional, in-person schools in Anaheim, Boulder, Hartford, and Charlotte. Online courses also continue to be a convenient solution for on-demand training. Nothing can replace real experience, but today, manufacturers really have no excuse for not connecting personnel with gear manufacturing knowledge.
—Adam Gimpert, Helios Gear Products
We must continue to plan further and further out in advance, the required skill set is not immediately available in the marketplace. We have seen success in hiring young employees and providing them with the time to learn the technology properly. Of course, this launch period is closer to two years instead of six months, but the employees see our investment in them and in return reward us with loyalty. Each summer we host apprentices in the States for 4 weeks, we take them to customers and provide them the opportunity to experience what the US has to offer, the hope is in three to five years they will be interested in relocating here if/when an opportunity arises.
—Shane Hollingsworth, Kapp Niles
Liebherr made a huge investment in our training academy—a separate section within our factory in Kempten, Germany—back in 2021. Called the “Machine Training Center,” nowadays this academy is used for our workforce development (for example training our service technicians and application engineers), but also used by our customers and end-users of Liebherr gear machines all over the globe. Both hands-on and in-person training programs take place, on actual gear machines, but also via online and digital training (live as well), further enhanced using the equipment found at our academy.
—Scott Yoders, Liebherr
We do not see any significant changes from 2023; hands-on training, particularly in the application, service, and support of today’s most modern gear machines, along with similar training for the “legacy” machines, is mandatory.
—Kenneth Flowers, MTB
NMTA continues to offer Gear Basics training. This has been very popular, and many companies bring me in to train new team members. Despite the popularity and efficiency of online training, live, in-person training is still relevant and valuable.
—Dwight Smith, NMTA
Star SU continues to place an importance on the education of our customers, from the aspect of our specific machining applications and a general understanding of gear industry knowledge.
—Andreas Blind & John O’Neill, Star SU
What level of focus is on IIoT and Industry 4.0 or 5.0?
IoT/4.0/5.0 solutions are already part of our regular development tasks and daily production life with design to manufacture solutions, Closed Loop and Smart Loop Manufacture with in-process quality inspection, as well as digital twins that allow to forecast feasibility of manufacture to avoid costly errors and scrap production. The highest precision and maximum efficiency must be built into today’s products, whether we offer design and simulation solutions or manufacturing cells with integrated quality inspection systems. It is something customers expect, and we continuously challenge ourselves to take fresh and new approaches to these requirements throughout the complete process chain.
—Christian Albrecht, Gleason
I feel the level of focus is much the same as the previous year, where mostly large companies are devoting relatively modest resources to develop technologies that fall under the banners of IIoT or Industry 4.0. Most manufacturing companies, which largely include small- to medium-sized operations, might have a few “pet projects,” but when simple automation (for example) is a “big step” for these manufacturers, the benefits of IIoT are still on the horizon.
—Adam Gimpert, Helios
Liebherr dedicated a huge number of resources to the IoT realm already starting six years ago, and nowadays we offer a complete suite of products to link, and collect data from Liebherr machines, other machine tools from industry, gear metrology equipment, and even automation. Our LHWebPlatform is the perfect basis to collect data in a standardized format (as well as offering the possibility to customize it to a specific need) with our LHSignalInfo, LHMachineInfo, and LHReportInfo system tools. We have enhanced these offerings recently on LHSignalInfo, to be able to complete adaptive process monitoring—often being able to detect problems in the production of gears—before they arise.
—Florian Schuon, Head of Digital Solutions, Liebherr; liebherr.com
This is most important for the OEMs that we support. Investment in the factories of the future is impacting how competitive the machines we represent are, relative to their designs, delivery, and cost. Our OEM partners recognize that—and we’ve picked some good ones to represent.
—Kenneth Flowers, MTB
I’m surprised by the relatively slow implementation of IIoT. This is especially true in the job shops where they need a concrete ROI in a short time. Many of the larger companies struggle with analyzing and transforming the data into actionable knowledge.
—Dwight Smith, NMTA
Our continued focus is to utilize IOT and Industry 4.0/5.0 where applicable.
—Andreas Blind & John O’Neill, Star SU
Do you have new workforce development solutions for 2024?
Like the whole industry, we face labor shortages of different levels depending on the geographic area we operate in. In some countries, we develop our workforce through apprenticeship and trainee programs. In others, we attract talent by a more diversified approach. Nonetheless, the topic remains a challenge and we are optimistic about the further development at Gleason.
—Christian Albrecht, Gleason
We are focused on making the seamless transition from an older generation of highly experienced technicians and professionals to a younger generation of less experienced, but very capable, individuals—and then training them to succeed. The labor pool is short, alarmingly so, of the skilled technicians, machine operators, engineers, and the others that we took for granted some 35 to 40 years ago. There is simply no alternative to establishing robust training programs in-house since there are very few technical schools or formal education available anywhere in the US for machine tool technology/design and manufacturing.
—Kenneth Flowers, MTB
Yes, we have implemented additional training for our service technicians to ensure they have the advanced skill set needed. For example, our mechanical specialists are receiving electrical/electronic training to broaden their abilities for machine repair.
—Dwight Smith, NMTA
As a global company, Star SU faces the same challenges that our customers and competitors face. Measures are in place to further training, education, and promotion of our internal resources.
—Andreas Blind & John O’Neill, Star SU
Is e-mobility heating up or cooling down in 2024?
While significant investments have been made in the past years, we believe that e-mobility still bears interesting opportunities regarding program extensions and ongoing investments in the automotive sector. We also see the upscaling trend for vehicles with larger drives and similar applications which join the general electrification trend. Electrification is not over—by all means.
—Christian Albrecht, Gleason
E-mobility is cooling down a bit. I just don’t see the infrastructure to support it yet.
—Claudia Hambleton, GMTA
Heating up! We’re at the cusp of the electrification of so many types of vehicles, and gears will be critical to these new systems. We continue to address the gear manufacturing needs of both startups, established EV makers, and their subsuppliers.
—Adam Gimpert, Helios
We still this as the main driver for automotive investment activity, projects are quite regular, and requests for future programs are consistent. Development demands are still very high considering we are almost 10 years from the initial technology that was developed. Our customers continue to push for methods of control and data collection, not only from grinding applications but connecting that information and analyzing it with various forms of inspection. This topic can feel like looking at an iceberg, the possibilities below the surface are many, and prioritizing these to meet customer expectations. As soon as you feel one step has been taken, we see another three or four to enhance the solutions further.
—Shane Hollingsworth, Kapp Niles
We suspect it will cool down in 2024. The unbridled enthusiasm and increase in sales and production in 2023 is now being tempered by the realities of the marketplace. Huge problems with infrastructure, sourcing materials, and the natural resistance of the consumer to high cost and impracticality are the current EV landscape. The ambitious plans and projections of the Big 3 for EV are already off the table. Closed plants and scaled back production are the reality near term.
—Kenneth Flowers, MTB
I see e-mobility cooling down slightly. We are seeing EV and hybrid projects in the planning stage. With the recent slowdown in EV sales, some of these may be delayed as the market adjusts.
—Dwight Smith, NMTA
E-mobility will continue to heat up, and we anticipate a steady growth of additional companies entering the prototype, installation, and development, along with established OEMS entering production phases.
—Andreas Blind & John O’Neill, Star SU
Where is the focus on energy and sustainability in 2024?
While we continue to maximize the efficiency in our operations, providing products with excellent productivity ratings and minimum carbon footprint, living up to ever-increasing official regulations and customer initiatives is challenging. To comply with such expectations, we improve supply chain management regarding its overall sustainability and minimize its footprint. It is a serious and tedious task.
—Christian Albrecht, Gleason
Sadly, lacking in every industry.
—Claudia Hambleton, GMTA
Despite what some might have us believe, it’s becoming increasingly clear that the drive to replace fossil fuels with clean energy can’t be achieved through electrification, wind and solar alone. The economic consequences would be ruinous. This will instead require a full court press, including hydrogen, nuclear, geothermal, bioenergy, and of course wind, solar and natural gas, along with a more gradual transition away from oil and gas.
—Kenneth Flowers, MTB
It is interesting that we read about this in the news and industry press, but don’t see much actual impact on the day-to-day operations of our customers. The hype exceeds the reality.
—Dwight Smith, NMTA
We as a company are constantly evaluating our current practices and strive to reduce our global carbon footprint. Measures such as facility upgrades (i.e., lighting, mist extraction, and central cooling systems, etc.), recycling efforts, modernization of legacy equipment, and utilization of solar energy.
—Andreas Blind & John O’Neill, Star SU
What is something I may have overlooked that is of great importance to you in 2024?
2024 so far, has not been a bad year. As we have pointed out before, we may feel effects of global crisis, overregulation, weak markets, and declining production, nonetheless, we feel optimistic about 2024.
—Christian Albrecht, Gleason
What is the age of the respondents or workforce in the survey? Most were corporate management or design engineers. I’d be interested to know how close they are to retirement and what legacy/recruitment plans they have in place, if any.
—Claudia Hambleton, GMTA
Since coming out of the pandemic, it feels that timing to SOP has condensed. The tools that design engineers have today allow for significantly more analytics before a beta build, hence we see the time from design to SOP is accelerated. The new normal is not a 5-year launch, it’s maybe 24 months and customers have 12 months or less from actual design release to production start requirements. The power of technological development can be seen in this area and many others. If I can add another point to this question, what is the future of re-shoring activity? We have seen in several areas, not a huge wave, but it is present and ongoing. I believe this topic ties into one of the survey questions about managing supply chains and government requirements. How long will this continue and to what extent is yet to be known.
—Shane Hollingsworth, Kapp Niles
The political landscape and the impending 2024 elections are of utmost importance. While the economy has seemingly weathered the short-term impact of the pandemic, serious longer-term challenges are mounting. The true economic state impacting purchasing labor and taxation, as well as the immigration situation and border crisis, will, if not remedied in Washington, weigh heavily on our jobs outlook and economic future.
—Kenneth Flowers, MTB
|
How is the push toward ELECTRIFICATION affecting your business?
“No effect.”
“New machine purchased for delivery in March 2025 has full automation. Seeking to add automation to hobbing machines.”
“Quantity of gears will reduced because numbers of gears have reduced in EV vehicles.”
“We are adjusting our product line to accommodate electric vehicles.”
“As an oilfield service provider, our customers depend on their volume of production sales. Electrifying vehicles reduces the demand for fuel. It puts a strain on oilfield equipment repairs. The same applies to the auto mechanics. We find it hard to support our families.”
“It’s given us new opportunities to explore.”
“The trend is there but due to product mix it did not impact last year.”
“Very positive.”
“Higher roughness requirement.”
“Need to make more investments related to new technology and slowly reduce old business.”
“Positive.”
“None.”
“Has not affected our business.”
“More motors means more gearboxes to rebuild.”
“It is not affecting our business in any meaningful way.”
“No change.”
“Substantially, with a level of uncertainty.”
“Has not been affected at all.”
“Not.”
“Impact of stray current is a growing concern.”
“Increasing customer investments.”
“No change yet, but expect it to augment growth for gearing technology as motor adoption continues to grow.”
“It’s terrible. Nobody wants electric vehicles except the garbage truck buyers...”
“Minor. Our industry is too remote to make full electrification feasible. Higher interest in hybrid solutions.”
“Don’t know.”
“In some applications, electric drives require higher input speeds, which changes the design of the products resulting from noise/vibration.”
“Slowing it down.”
“Making us consider new directions.”
“To some extent it’s affecting us negatively—approximately 4–5%.”
“Reducing target clients.”
“We are the last to make a change and not forward looking.”
“It is a really good opportunity.”
“Providing new opportunities for product creation.”
“We are now producing gears for e-transaxles for electrified vehicles.”
“Not applicable at this time.”
“Very little.”
“Increasing.”
“Yes, it does affect...but getting compensated by tractor and construction equipment volumes.”
“Big .”
“It has impacted certain customers completely, but as we provide complete drive systems, we are still able to compete.”
“None.”
“Nothing.”
“More EVs = Less Gears.”
“None.”
“Getting ready for electrification components.”
“Not much.”
“No effect.”
“Not at all.”
“High.”
“It is not (so far).”
“Not—we are not involved in automotive.”
“We are into EV transmission mainly.”
“The requirement for more precision and silently operating gears has increased exponentially to be attained at very high costs.”
“Hurting .”
“Until 2024 nothing.”
“Slow.”
“No effect at this time.”
“Not very much.”
“Negatively.”
“Not at all.”
“Increased opportunities and adoption of new technology.”
“Medium.”
“Market trend is not clear, affecting the investment plan for the next years.”
“Big effect on design requirements.”
“No major effect.”
“Gears are not needed in some applications anymore.”
“Business will increase for precision gears.”
“Electric vehicles usage is increased. The new startup companies in the electric sector are growing much faster than earlier.”
“Is not affecting .”
“It typically has little impact.”
“Have not seen any major impacts.”
“This impacts us with the mining trucks sold, which has been very strong and looks great over the next 5 years and beyond.”
“Not much as yet but expect that it will in the near future as we see more applications at higher load/speed combinations.”
“Electrification requires high quality gears. Gear metrology is more important.”
“Bad influence.”
“This affects us very positively.”
“There is no effect.”
“We’re in the process of converting most forklifts and tug carts.”
“Very little impact as of yet.”
“Non existent and losing steam.”
“No effect.”
“Not significantly at this point.”
“Only that our concern for how this electricity will be produced.”
“Not applicable.”
“Was strong, now focusing on other core industries.”
“It’s forced us to improve of the use of simulations in development stages.”
“More interest in hybridization. Pure electric operation is not currently feasible for our industry.”
“This is the main reason for our increases in business levels.”
“Massively.”
“N/A yet.”
“Huge. As long as we can keep up with demand.”
“We are ready and involved.”
“None.”
“Minimal, although keeping an eye on market trends.”
“Not at all.”
“We have added electrical and automation engineers to our staff and products to our portfolio.”
How are you handling and navigating supply chain issues heading into 2024?
“Day to day.”
“ID/OD grinding support continues to be a capacity issue with our vendor base.”
“By diversifying business to suspension and steering.”
“Carefully.”
“We are doing our best to promote ‘Made in America,’ even if it requires Americanizing Chinese Reducers. We are replacing Chinese gears with specialty-designed American gears and converting the Chinese reducers.”
“Getting everything we can out of China.”
“Depending on need. No big issue now.”
“Long term contracts with suppliers—increasing our stock.”
“Evaluating different countries for changing the supply chain.”
“By making alternate sources, and in-house capabilities.”
“Expanding search for more partnerships in supply chain relationships.”
“More inventory.”
“There are no significant problems at this time.”
“With greater ease than 18 months ago.”
“With a certain level of frustration.”
“We have no supply chain issues.”
“Prayer. Long lead times!”
“No problems with supply chain.”
“Diversification and better management tools.”
“Terribly.”
“Diversification, continuing to reduce reliance on China and developing alternate sourcing for U.S.-based suppliers.”
“Freight rates are being passed on.”
“No major issues.”
“No worries.”
“We are tapping other additional opportunities.”
“Struggling and sending parts late.”
“We see no problems on this topic so far.”
“Supply chain has settled down and is returning to normal.”
“Conflicts between countries are directly affecting us.”
“Improved planning, partnering, and communication.”
“Our supply chain has been surprisingly easy to navigate other than increased cost. Quantity hasn’t really been an issue.”
“Not an issue.”
“Challenging, as there was some dependency on long-distance suppliers, which are being navigated through strategic sourcing from within 100 km distance. It is proving effective but challenges on quality remain.”
“More direct contact and follow up with suppliers.”
“Holding steady/same.”
“Double- checking long lead items with machine suppliers.”
“So far no major issues.”
“Increasing inventories on material.”
“All is good now.”
“Finding new suppliers out of state.”
“Not really an issue for us.”
“Mainly suppliers all located in Japan, so at the moment no severe problems with material supply.”
“Working with vendors to better communicate trends, being selective on who we deal with.”
“More on predictive buying and cooperation of suppliers.”
“By planning in advance, by maintaining expected requirements from customers.”
“We can´t see problem to our planning in 2024.”
“New ERP system.”
“Ordering more, stocking material, trying to get volume pricing.”
“Using more help from freight forwarders.”
“Digitization .”
“Have a shorter and nearer supply chain.”
“Sourcing of special steels is still a problem and also the unfortunate price increases on a daily basis.”
“Better than last year.”
“Sourcing from close and reliable origins.”
“Input costs have gone up. Price revision, value added services to customer to compensate for the increased cost.”
“Localization and increasing the quantity of suppliers.”
“As normal.”
“In-region strategic transfers. In-load to our facility.”
“Patience and prayers at this point. Communicating issues with customers as best as possible. Buying future material runs.”
“Lead times are coming down, so this seems to be fine. Aerospace material grades don’t have many options. Pricing is very high and lead times are very long.”
“Much better than the last three years where electronic components were so difficult to get, and delivery times unstable and unforeseeable. Now we feel and see that this problem is much less acute.”
“Shift the delivery.”
“Working with suppliers to prevent any future supply chain issues.”
“We have adjusted well and have very few issues in our supply chain..”
“Planning and forecasting improved.”
“Not a problem.”
“Supply chain is flowing well.”
“We need to search around the world for better conditions for the supply chain. We are investing in supplier qualification.”
“Continuing to expand presence in Europe, divesting from the United States and China.”
“We are struggling with vendor lead-times. Many times the lead-times for very small parts is greater than the lead-time for one of our multi-1K ton machines.”
“Increasing the level of engagement of most important suppliers.”
“Cautiously.”
“We’ve been lucky.”
“Was challenging, but issmoothing out.”
“No change.”
“Watching closely to catch trends before they get bad like 2020/2021.”
“We don’t have a problem.”
“Starting to see shipping issues again, but nowhere near to 2021 levels. We are looking into alternative routes.”
How is your organization addressing the skilled worker shortage?
“Training staff and middle management.”
“Better equipment and adding automation.”
“Regular new trainees and training them as per our requirement.”
“We have relationships with multiple universities. “
“In the gear industry, we have to spend years training our technicians.”
“Training and working with local schools.”
“Training new and young people.”
“Difficult topic. Til now we are finding the right people—but it takes longer time.”
“Not much.”
“Try to retain old employes. Upskill junior level employees.”
“Automation wherever possible.”
“Hiring younger.”
“Increased internal training resources to create the skills. Also investing in technology to reduce reliance on skilled labor into the future.”
“We are trying to keep our current quality workers. But it’s taking longer to get new talent on board.”
“Using a partial non-migrant workforce.”
“Not very well. Recognition is slow in coming.”
“We are retaining our employees .”
“Much prayer, but maybe not to the correct deity. I’ve been in gears for 50 years. The biggest hurdle is management, because to bring a young engineer up to a level to be competent in gear unit design and engineering is five years with proper mentoring. A competent machinist about two years. A competent service man 3–5 years. The management philosophy is: Go hire someone today, they can start in two months, if they pass the hiring process, then they will be ready to go. The new people needed to be hired five years ago. Oh yes, pay!”
“We are not having a skilled worker shortage in the Greater Toronto area.”
“Investing in community development programs, investing in more job training programs, and automating what makes sense.”
“Increased compensation and benefits, increased internal training and opportunities to move within the company.”
“Hire and train and pay enough. Nobody thinks they can compete on compensation.”
“Trying to automate as much as possible.”
“Workers are being trained or reimbursed for college classes.”
“Training like crazy.”
“Training new employees.”
“We are not. We have a lot of old employees and no good way to fill the gaps.”
“We make people grow from the bottom. Nevertheless certain positions are difficult to cover.”
“Hiring bonuses.”
“Keeping talent motivated and rewarded. Generational changes are now more drastic with actual centennial people vs millennials and X, Y generations.”
“In-house training.”
“Recruiting heavily and attempting to automate wherever possible to reduce requirement of workers.”
“In-house training team with amazing capabilities.”
“Poaching is there to stay, and we are treating skilled workers as our own assets.”
“We have partnered and suggested our supply chain also partner with local schools and universities, basically bringing the apprentice program back.”
“Outsourcing.”
“Hope and a prayer. Refuse to develop or bring in young people. Keep holding on to “a hope and a prayer” to find experienced gear machinists. Need to bring back apprenticeships!!!”
“Training in house.”
“People are stable in their jobs, so far.”
“Still struggling.”
“Internal training programs.”
“In-house training.”
“Trying to do in-house training.”
“Continuously conducting interviews with possible candidates and improving the skills of unlearned workers through on-the-job training.”
“Poorly—we are having trouble retaining good people and finding replacements.”
“More on automation and de-skilling. For skilled worker, giving more opportunities and upgrading semi-skilled by training.”
“By adding fewer but people skilled in multiple areas and by training not-so-skilled ones in house under the guidance of the skilled workers.”
“With much difficulty because entrants to the metal industries are less available.”
“Internal training. Training local workforce.”
“Own internal school.”
“Upgrading equipment.”
“Society offerings of training, local junior college or trade school.”
“Training.”
“Training by using VR/AR/MR platforms.”
“Work in partnership with technical schools.”
“Automation.”
“I don´t know.”
“We have employed a new machinist in the gear cutting department to train and upgrade our output and quality.”
“Increasing the ability of current ones.”
“Training. Employees work in various positions. Promotion in universities and schools.”
“Training new candidates.”
“Training and skill development.”
“Increasing the trainees and providing the on-the-job training to them after systematic training courses.”
“Using CNC equipment.”
“There’s no way.”
“IT support.”
“Resource pooling, tie up with universities.”
“Apply new technology.”
“Push towards automating properties.”
“Working to improve our culture to keep people longer.”
“No problem as we are a small group who have all worked together for more than 55 years!”
“Apprentices (dual study).”
“No skilled young people available. Old people are still useful!”
“Offering competitive salaries and benefits in the market and a pleasant work environment to retain our staff.”
“In-house training programs.”
“Looking to sponsor out-of-country candidates, looking to education system for apprentice opportunities.”
“Junior colleges, recent military separations.”
“More focused hiring.”
“Reaching out to community partners for help in identifying and hiring employees.”
“Not a problem for us.”
“Focusing on internal skill-based training program and versatility training as well for longer term employees.”
“Exchanging skilled workers of the company located in different plants.”
“Internal training, women in trades, coop programs, increased compensation and benefits.”
“Working with local tech centers and colleges for their upcoming graduates. We are hosting many manufacturing visits from the local high schools.”
“Increase internal training capacity and attitude, expand company’s benefits to create employee loyalty.”
“Training.”
“Automating more, hiring less and upskilling.”
“Lots of interviewing.”
“It is extremely difficult to find professional help these days. We are on a constant look for a proper fit to our company.”
“No major issues this year after a rough 2023. Wages and extra recruitment efforts were needed in 2023.”
“Very hard to get young talent to do this type of work.”
“Looking to launch a formal apprenticeship program.”
What role will emerging technologies (including, but not limited to IIoT, additive manufacturing, robotics, automation and artificial intelligence) play in your organization in the coming years?
“We are introducing robot automation.”
“Likely a much bigger role.”
“Reduction of manpower due to increase of automation.”
“Additive manufacturing of many of our lower stressed components.”
“The CNC Microsoft new technology used in the Five Axis Machining Centers is revolutionary. But for the small business, it is priced at a level that only the prime contractors can easily afford. We (the small business) will continue with the conventional method.”
“IIOT is an excellent tool, as is six-sigma. We use both.”
“We are doing our best to work these trends toward our advantage.”
“Automation for part handling and workholding changeover up to 100 kg.”
“Important role.”
“Robot, automation and IIoT.”
“New software for documentation, gear calculation, online programing and auto correction makes process easier. And robots.”
“Automation of design activities will be carried out.”
“Little effect.”
“Lots of automation will be brought to the work order system.”
“We are investing now to understand the role...separate the hype from opportunity.”
“About the same as now, slow and steady.”
“Hopefully there will be a shift towards new and emerging technologies. But, that will require investments that are slow in coming.”
“We continue to add robotics to our operations.”
“We’ve got a lot of artificial intelligence. What we need is real, tangible intelligence, which takes a few years to have. LOL. That spark of creativity is very important.”
“Will have to be implemented.”
“Will be critical to help in reducing carbon foot print and increasing component life.”
“Reasonable role—depending on customer demand to incorporate.”
“A significant impact. Those who do not adopt emerging technologies will not be competitive.”
“Nothing can replace a hard American worker, properly educated.”
“Automation and autonomous systems will be a large part of both our manufacturing and products.”
“We see technology playing out in many different ways from internal changes related to manufacturing efficiency improvements, speed to market, and reduced downtime (digital twin-maintenance). On the sales side, we see similar evolution in our products and the market needs, which encourages a higher level of design integration.”
“We will be quicker to get products from design, through manufacturing, to the customer.”
“Yet to make any significant impact.”
“Low role.”
“We already utilize robotics and will need to better utilize them.”
“For sure the new technology will support us in growing.”
“Very limited role for emerging technologies.”
“Some in the near future, but likely more in the 10-year planning.”
“Robotics and automation will be most significant to us as we struggle to automate worker tasks. We have utilized AM in work holding for many years and are still ramping this up.”
“Robotics, small automation and single-piece flow are being implemented with focus on continuous improvement.”
“Big.”
“We have already begun additive manufacturing; robotics are starting to come into the field.”
“No impact.”
“No role.”
“None.”
“Low impact.”
“Potentially big improvements.”
“Need to stay informed.”
“No effect.”
“Probably not much effect in our markets.”
“High.”
“Not clearly statable so far. Probably noncritical to neglectable dimensions.”
“IIoT is already present; we are looking at additive manufacturing.”
“IIoT, AI, automation, robotics, machine learning.”
“We can venture into automated loading and unloading assisted by robotic arms and increase use of semi-automated robotic arms to help operators load and unload larger and heavier jobs.”
“None.”
“Little relevance. As much as possible we will try to implement additive manufacturing. This is not the time for big investments.”
“Some robotics are currently used and will add more if needed.”
“Slowly increase productivity levels.”
“Very little.”
“Lean digital technology.”
“A more automated factory using a sum of technologies. The factory will be able to work alone 100%.”
“We are a jobbing plant and are slowly moving more of our production off the older manual gear machines to the new multi-axis CNC machines and are looking to upgrade our gear grinding equipment, but costs are high.”
“Will have major effects.”
“Selling price is always under pressure.”
“Will have a positive influence and need to update the skill level.”
“Smart sensors as condition monitoring devices and SCADA will be the key element in every automated factory.”
“Do not affect us.”
“Additive manufacturing and robotics may help.”
“It will enhance our productivity and address our yield.”
“Only way to manage growth with current labor market will be automation and data monitoring.”
“Having the capex to invest in technology that many leaders do not see the importance in investment.”
“Important role.”
All this is already used since long time in our company. New tools are not always better. To do the same thing we were doing with 700 kilobytes now can’t even be done with 700 megabytes!”
“New technologies are and will be playing a leading role in this industry.”
“Robot and cobot implementation where possible.”
“Will maintain status quo. No large capital output.”
“Will most definitely increase and become more important over time.”
“Zero.”
“We’ll explore best practices.”
“We will be evaluating all these technologies and looking for the right fit.”
“No plans at this time.”
“Hopefully reduce the labor issue”
“We are doing partnership with universities to improve issues regarding technologies as IIoT, additive manufacturing, automation and artificial intelligence.”
“Huge push for preventative and predictive maintenance.”
“We are investing in all of these technologies.”
“A major one, very important impact.”
“We will invest in robotic arms vs more CNCs.”
“Incorporate more robotics.”
“No change.”
“Minimal.”
“Actually don’t know at this point.”
“Our mechatronic division is growing and we don’t see that slowing down.”
How will the gear market evolve in the NEXT FIVE TO 10 YEARS?
“It is going to grow.”
“Capacity in the gear market has been tight and I don’t see the demand for gears slowing up at all in the next 5–10 years.”
“It will be reduced 20 to 50%.”
“Geometrical precision and materials.”
“It will all depend on the direction the USA goes.”
“The need for new lubricants that are lower shearing.”
“The suppliers who continue to invest in people and equipment will gain market share.”
“Should grow.”
“We are working in precision gear business. Because of increasing automation levels, the market will grow.”
“Decreasing.”
“Gear market has become more competitive, and OEMs need more reliable gear manufacturing partners. Manufacturers needs to change manufacturing technology to overcome new changes.”
“The reduction in vehicle gearing due to electric automobile production will pressure gear companies focused only on industrial drives with more competition.”
“Low noise, highly optimized contact gears will further penetrate all industries.”
“More domestic purchases.”
“Unsure of the future at this point.”
“Most of the gear units will be made offshore, China, Korea, Germany, Brazil, Spain, India, maybe Mexico.”
“Simple gears will leave...”
“Increasing demands for longer gear life, with lower carbon footprint.”
“Decline in automotive sector, increase in heavy equipment.”
“Good question. I hope we have the courage to learn, invest in and adopt emerging technologies. If we don’t evolve, we will become obsolete.”
“Automation will play a big part, unfortunately. AI, automation and robotics.”
“Higher requirements: quiet gears for electric applications.”
“Fewer shops willing to do what we do, giving us a larger customer base.”
“High volume production of gears will be predominantly produced in low-cost countries. The U.S. and western world manufacturers will have to focus on technology to remain relevant as well as sourcing globally to remain competitive. While we will still see traditional machinery produced, we can anticipate no new development in traditional designs but a transition to electrification in every possible market.”
“Don’t know.”
“Slowly components for gear train for electrical vehicles are getting manufactured locally and expect this to improve with time.”
“I don’t know.”
“Fewer heat treating places to heat parts will create a bottleneck.”
“Will decrease in number of gears but increase in the quality. Therefore, better equipment and strategies will be necessary.”
“It will shrink slightly due to electrification, but will stay strong.”
“Less components purchasing, more accuracy on actual ones. Quicker product delivery because changes are happening faster now.”
“I would expect more advances in additive manufacturing, particularly in materials and property enhancement.”
“We believe to achieve increased loading in continuously smaller packages, that a fair portion of the market will go from traditional rolling element bearings to oil lubricated journal bearings.”
“Volumes might reduce, but accuracy and margins will increase.”
“Stay the same with changing applications.”
“That is the million dollar question that no one can truly answer.”
“Unknown.”
“I have real concerns companies will continue to try and offload gear manufacturing south of the border. Evolve is not the correct term, survive is.”
“Market will decrease.”
“Stronger quality for noiseless gears.”
“Continue to shrink because of lack of interest by young people.”
“Steady.”
“More 3D printed parts, new heat treat, new materials.”
“Lower volume of gears, but much higher requirements for NVH and tighter tolerances. Master gear quality for series production is the motto.”
“We expect some growth with fewer players in the marketplace.”
“More stringent on performance and noise level. More light weight and more torque with process improvement.”
“There is going to be a slight shift in type of requirement of gears, but the constant requirements will remain and only increase as the other countries look for alternatives to China production. The market will turn towards India for the same to achieve same quality and similar costs.”
“We don’t know.”
“Uncertain.”
“Don’t really know.”
“More automation, freeing time for current staff to improve quality, etc.”
“Immensely.”
“We suppose that small gears will be done with additive manufacturing, the big ones no.”
“I don´t know.”
“I would suggest that there will be a move to additive manufacture for smaller gears and conventional subtractive manufacture for large gears.”
“Less multi-speed gear boxes, more high-speed gear boxes.”
“Slightly increase.”
“Demand for precision gears will increase.”
“30% growth.”
“Improve 10% to 20%.”
“Growth of 10 to 15 percent.”
“For our specific products there is not much change, but on the processing side, we will definitely have changes that may help us in the next 5 to 10 years.”
“Large push to automation. Smaller companies absorbed into larger ones.”
“More automation and less importance on people and relationships. Developing new customers will get harder and harder.”
“More attention to gear noise.”
“No idea.”
“Only high-quality gears will survive with large dimension gears.”
“With each passing year, higher quality gears will be required to satisfy new quality requirements.”
“Precision gear grinding and hobbing with automation.”
“Not really certain...”
“More electric drives, hydrogen powered drives, greater automation requirements, more AI features and additive technology improvements.”
“Decrease.”
“Should increase.”
“It will continue to get more complex in terms of the machinery and the training level to maximize the return on investments.”
“Don’t have a clue.”
“Globally gear technology is getting stronger and will make it tougher for North American companies to survive.”
“In my opinion the market regarding gears will grow maybe 40% next years, but new subjects will come around such as lubrication, heat dissipation, high speed, low weight and NVH.”
“It is likely that lower demand will create the opportunity for focusing on improving the gears quality.”
“Room to grow.”
“Eastern Europe will become a major source of manufacturing provided the Russia/Ukraine conflict doesn’t amplify...U.S. market will continue to struggle with labor and talent. China will begin to implode under their demographic shift as workers can’t be born quickly enough. Higher quality will be standard due to NVH limits becoming stricter after electrification.”
“Not easy to foresee.”
“It will be completely automated manufacturing.”
“See moves to higher quality parts and continued push to keep costs low.”
“I think it will improve.”
“More mergers causing some brands to become legacies. Repair market will grow as it becomes sustainable to push repair vs. replace.”
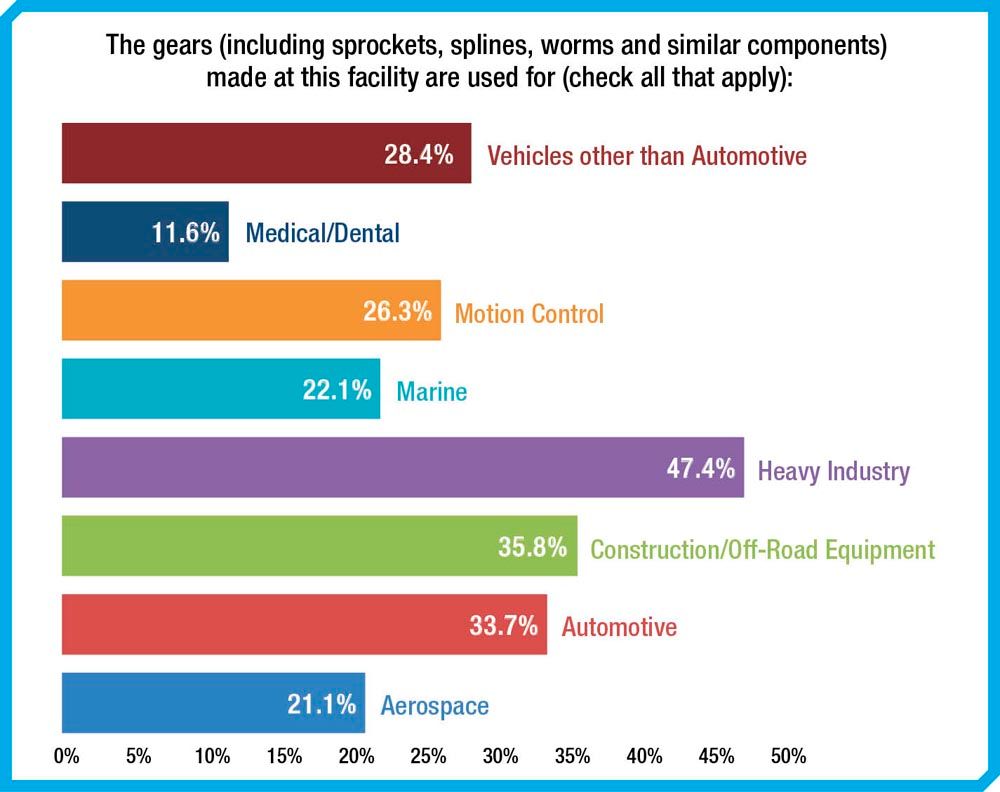
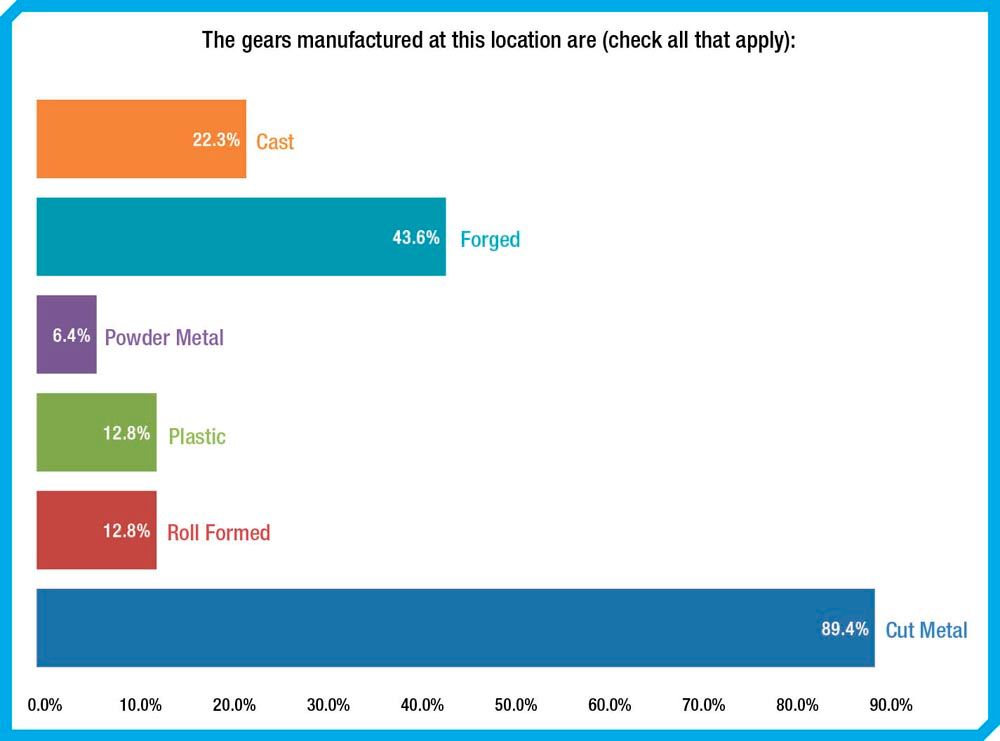
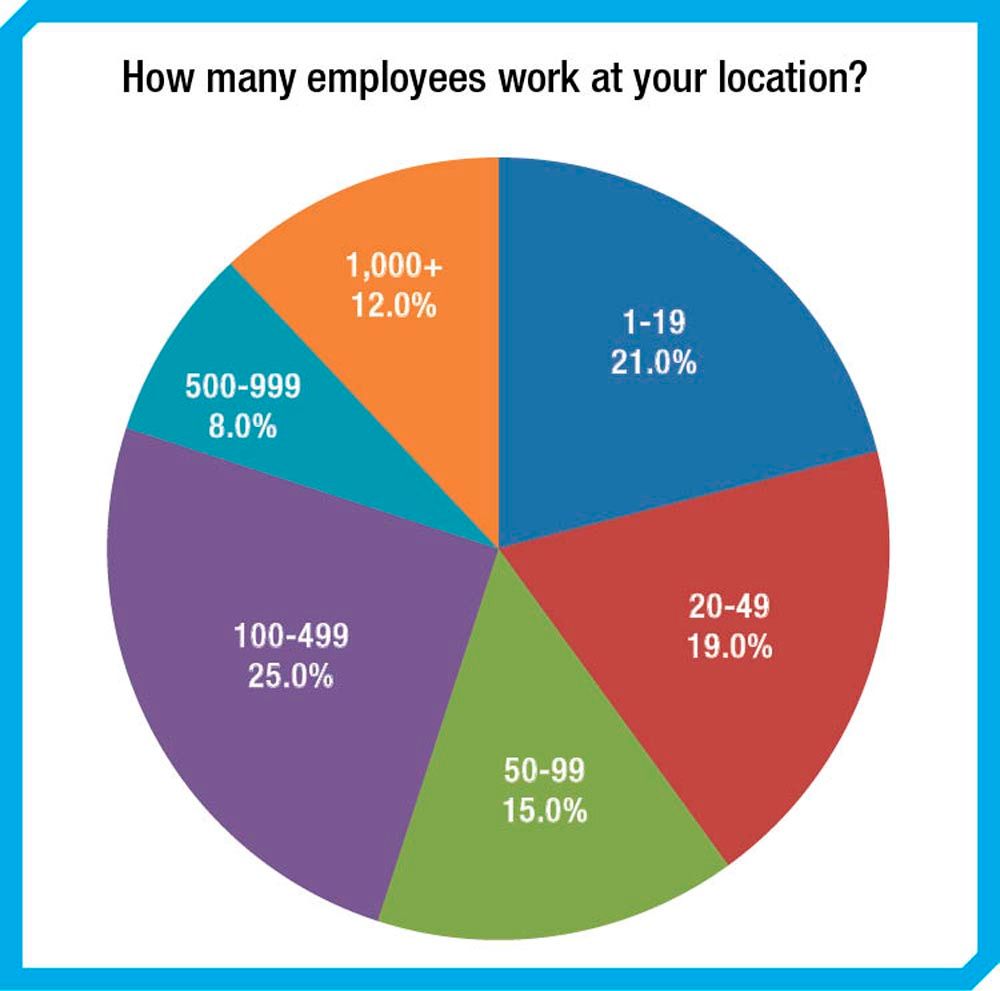
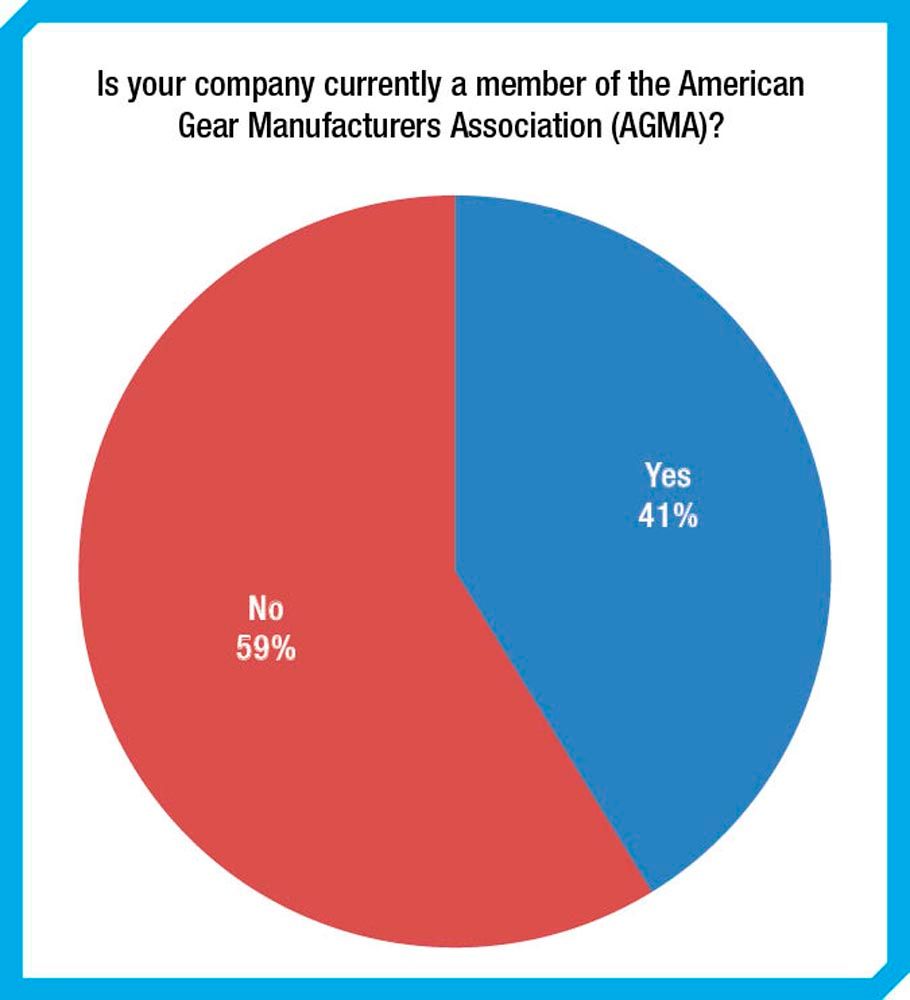
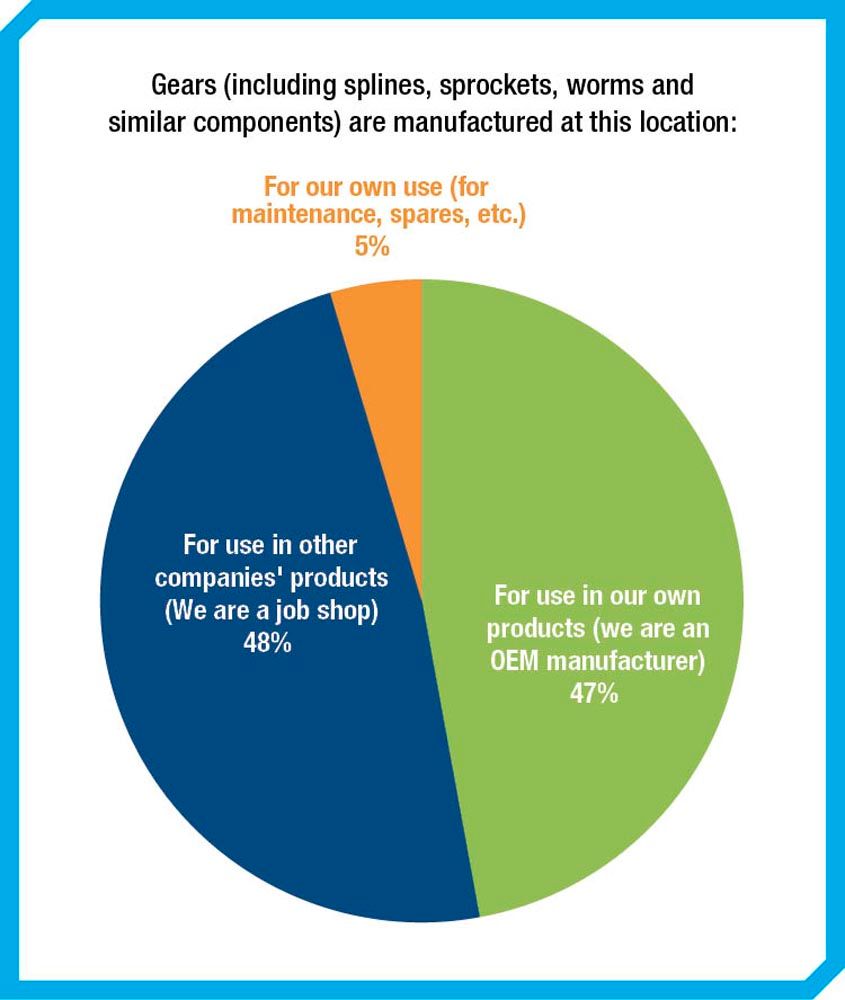
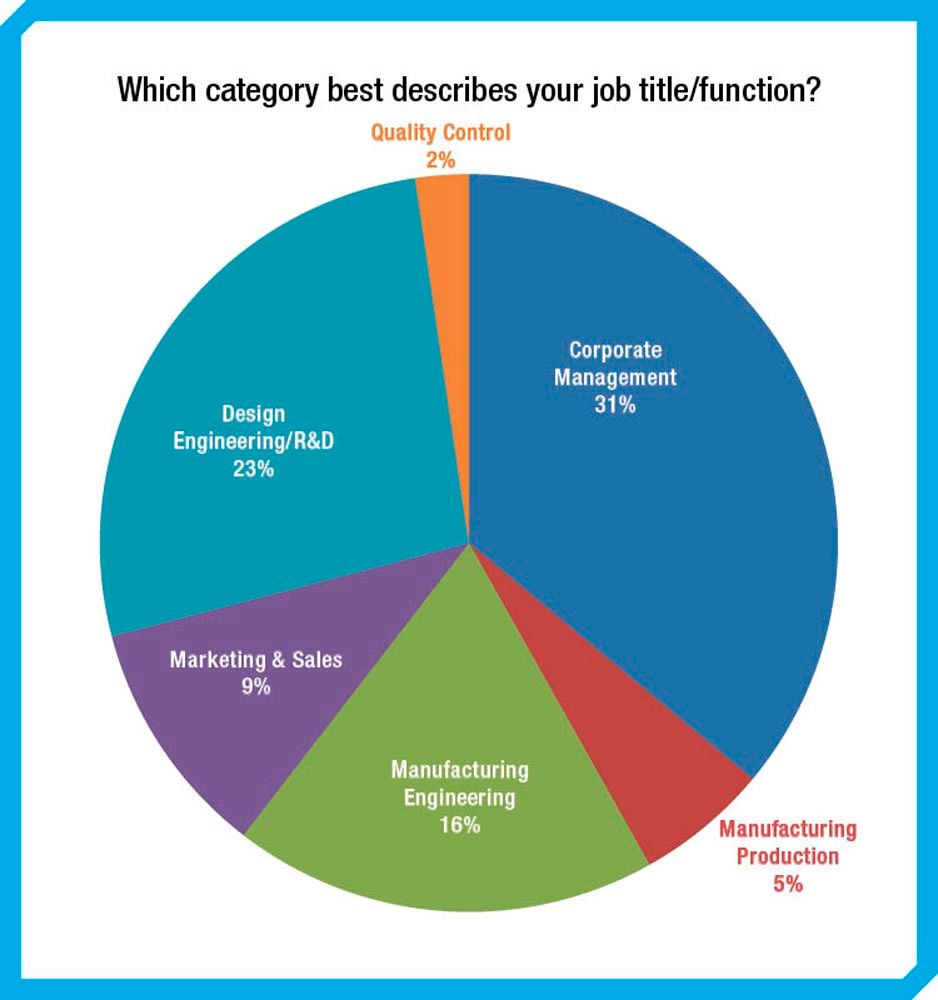
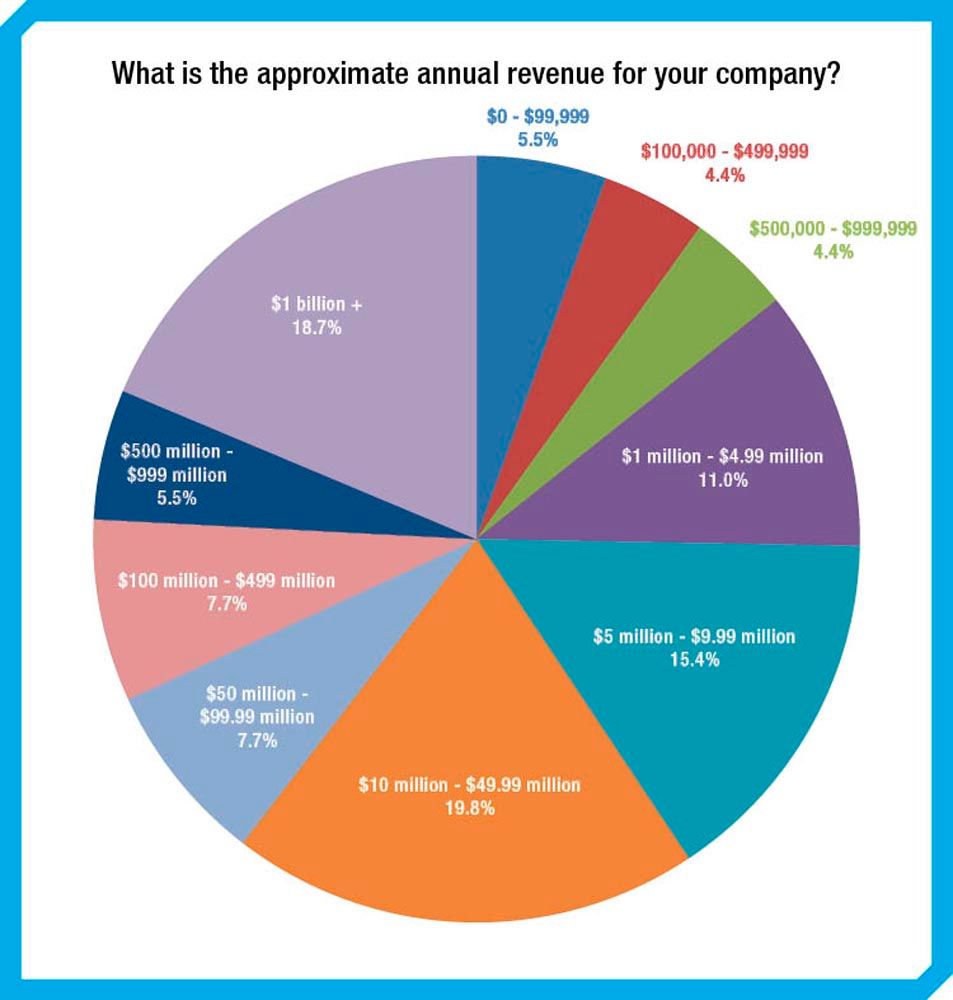